What material is best for an RC Plane? Post 1
- Joel Runevic
- Oct 14, 2019
- 4 min read
Updated: Nov 1, 2019
RC Plane Post by Hassan Bajwa and Joel Runevic
Introduction
Over the summer, we decided it would be a very interesting experience to build a remote-controlled (RC) plane from scratch. Not only does this allow us to have a more hands-on approach to physics, but there is a lot of theoretical physics that we can apply during the construction of our plane. This is the beginning of a series of posts that will, in detail, explain how we went about the project. This first post focuses on the decision-making process that went behind the selection of the material for our plane. Feel free to contact us if you have any more questions on how we went about building our plane.
Deciding on a material
During our initial discussions after deciding to create OnlyPhysics, we spoke about what our first project ought to be. Very quickly, we agreed that we would greatly enjoy the challenge of constructing, from scratch, a remote controlled fixed-wing aeroplane, designed very similar to the one shown below, which is a German Air Force Transall C-160D. We would purchase electrical components that we were not able to build ourselves, as well as a material with which to build the fuselage and wings. But we were to design and assemble everything with as little guidance from the internet as possible, while restraining ourselves to stay within our budget, which meant buying cheap but reliable electronics. This is a log of our progress throughout the procedure.
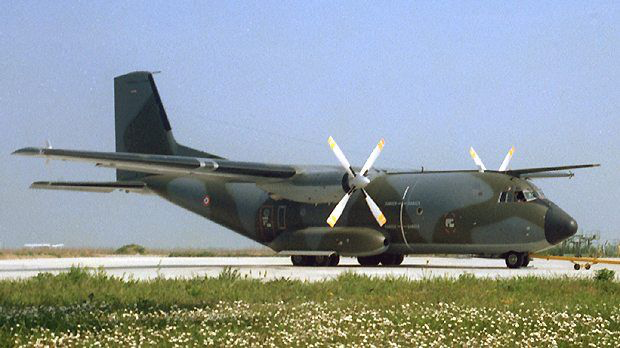
The first step was to narrow down our idea of a ‘remote control plane’ into a more channeled, specific design. The easiest way to achieve this as a team was through Skype video calls, which started off with us deciding the way in which the plane would be built. Unanimously, we figured that a twin-propellor, conventional-tail aircraft would be the ideal design to base our aircraft on. Furthermore, we would use a Clark-Y airfoil for the wing profile. One of the first problems we encountered was the choice between spruce, balsa or expanded polypropylene as the material of our choice. We used the table below to help us in this choice. Due to limited information on EPP, we decided to use HPP (homopolymer polypropylene) as a proxy for some values (where stated). We made this decision because we felt trying to find exact data on EPP may hold us back when HPP was relatively similar and we had some data readily available.

Average Dried Weight: a measure of a material’s weight in relation to a preset volume, and in relation to wood, specifically at a 1% moisture content, where for context 12% is equilibrium moisture content (EMC), or the moisture for a wood which has been exposed to air for a long time. This is important for us because a heavy wood makes us require a little bit more power to make it airborne, and thus a strong yet light wood is ideal.
Specific Gravity: a measure of the ratio of a material’s density as compared to water, at EMC. For us, this is another way of determining the weight of the fuselage of our plane.
Janka Hardness: the force which must be applied to sink a metal ball (diameter 11.28mm) 5.64mm into the wood. This is a quantity specific to wood, so there is no value available for polypropylene. This is useful for determining crash resistance - a higher Janka Hardness means that our plane will be able to withstand a larger impact in the event of crashing.
Flexural Modulus: the stress exerted on a given material just preceding yield point. We don’t want a wood that will break under a low force so a higher flexural modulus is desirable.
Elastic Modulus: the tendency of a material to deform along a given axis when opposing forces are applied along it. This provides us with an indicator of the strength of each material.
Compressive Modulus: the ability of a material to resist loads attempting to reduce size, or compress, as opposed to elastic modulus. This modulus is useful in gauging whether our plane will deal with our loading (the components).
After reviewing the data in the table, we eliminated spruce on account of its weight being too great for convenience in a small-scale aeroplane. Even though EPP arguably outperforms balsa wood for many aspects, the differences are mostly marginal - combine this with a high cost for EPP and balsa wood’s reputation for being easily craftable (don’t forget we had to carve a block into a fuselage with minimal woodwork skills), and balsa wood was becoming the more likely of the two materials. Upon sourcing a 75 x 100 x 450mm block for under £20, we had decided that our main material would be balsa wood.
That is it for the first post on our project. Thank you so much for taking the time to read this. As we have already finished the project, we will be uploading more and more posts shortly, so stay tuned! Feel free to ask any specific questions, especially if you are interested in building your very own RC plane.
Comentarios